Da Johnson-Fluiten un giunto rotante customizzato per migliorare le prestazioni dei cilindri stacco-stiro
La collaborazione fra Johnson-Fluiten e l’ufficio tecnico di un costruttore di impianti ha rivelato la possibilità di modificare i giunti rotanti in uso per migliorare l’efficienza del macchinario. Si è trattato di un lavoro di équipe che ha richiesto uno studio accurato, unito alla capacità di pensare fuori dagli schemi. I risultati hanno ripagato abbondantemente le energie e la creatività impiegate per portare a termine il progetto.
I fornitori di componenti per la gestione dei fluidi realizzano prodotti adeguati alla maggior parte dei costruttori di macchinari, ma non tutti sono in grado di personalizzare le proprie soluzioni in modo da conformarsi perfettamente a specifiche necessità applicative, garantendo benefici concreti e misurabili.
Johnson-Fluiten ha una lunga storia di successi in tal senso: fra i casi più recenti, la realizzazione di un giunto rotante speciale per un’importante azienda internazionale produttrice di macchinari per la lavorazione della plastica.
Macchinari complessi
Il costruttore utilizzava già giunti rotanti Johnson-Fluiten per diversi impianti: la loro versatilità permette un’integrazione facile in vari tipi di macchinari, come calandre, preriscaldatori, gruppi alzatrice, goffratori, raffreddatori e cilindri stacco-stiro.
In quest’ultima tipologia di impianti, i giunti rotanti vengono montati in modo da erogare i fluidi che regolano la temperatura del cilindro, consentendo lo svolgimento delle diverse fasi di lavorazione della plastica. Si tratta di giunti a gomito che devono avere una perfetta tenuta meccanica per convogliare il fluido mediante una parte rotante; è necessario inoltre che sia possibile sostituire facilmente la tenuta meccanica interna in modo da poter utilizzare diversi tipi di fluido – olio diatermico, acqua surriscaldata, acqua per il raffreddamento – senza modifiche alla linea di produzione.
All’interno del catalogo Johnson-Fluiten il cliente aveva selezionato i giunti SX prodotti da Kadant, ai quali applicava delle teste di montaggio dall’ingombro ridotto, realizzate dal costruttore stesso per inserire i giunti nel macchinario: le prestazioni dei giunti erano ottime, ma l’adattamento degli attacchi di entrata e uscita richiedeva un supplemento di lavorazione che riduceva l’efficienza complessiva del processo.
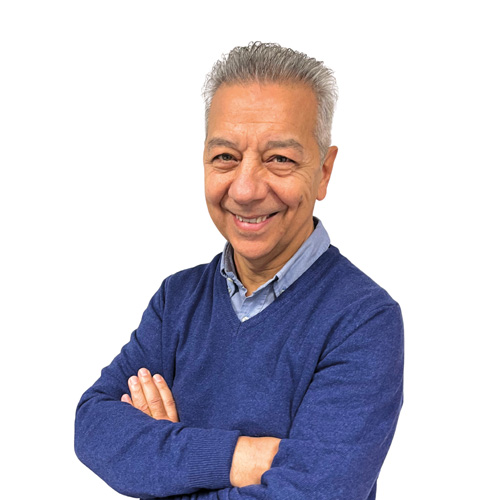
Un partner proattivo
Il rapporto di Johnson-Fluiten con i clienti non si esaurisce con la consegna dei componenti, ma prosegue per avere la certezza che le soluzioni fornite siano perfettamente adeguate e poter apportare eventuali miglioramenti se necessario. “Ci siamo resi conto che il giunto SX, pur essendo adeguato, non aveva la perfetta corrispondenza con le esigenze del cliente che siamo abituati a garantire,” ci spiega Ilvio Corigliano, Sales manager di Johnson-Fluiten.
Lavorando fianco a fianco con i progettisti dell’azienda cliente, i tecnici Johnson-Fluiten hanno studiato una soluzione che mantenesse i vantaggi del giunto SX – la possibilità di essere utilizzato con diversi fluidi, la perfetta tenuta e la manutenzione praticamente azzerata – eliminando però le necessità di adattamento in fase di montaggio. In considerazione dei volumi produttivi dell’azienda cliente, Johnson-Fluiten ha valutato l’opportunità di creare un giunto custom. “Abbiamo concluso che il lavoro di prototipazione, collaudo e produzione di un giunto ad hoc sarebbe stato un impegno più che giustificato dagli indubbi vantaggi che il prodotto finito avrebbe apportato al produttore,” prosegue Corigliano.
Progettazione personalizzata
Il team tecnico ha identificato una soluzione che ha permesso di eliminare ogni necessità di adattamento in fase di montaggio e di semplificare notevolmente questa operazione, aumentando la lunghezza del rotore di 20 mm e disegnando una testa completamente custom che fosse adatta alle dimensioni e alle specifiche della macchina.
In fase di progettazione, i tecnici Johnson-Fluiten hanno valutato la possibilità, a seguito delle modifiche apportate a testa e rotore, di impiegare un giunto RX al posto del giunto SX in uso: la nuova configurazione ha infatti reso possibile l’utilizzo di questo modello nonostante gli ingombri ridotti richiesti dai cilindri stacco-stiro.
L’utilizzo di questo componente si è rivelato particolarmente efficiente in questa applicazione: il giunto RX utilizza infatti cuscinetti anziché bussole di grafite, il che ha ridotto notevolmente l’attrito e ha permesso di ottenere la necessaria velocità di rotazione anche con un motore di minor potenza, permettendo un risparmio di energia.
Dopo i rilievi e i test preliminari necessari è stato realizzato in tempi molto stretti un prototipo per verificare che le dimensioni, gli ingombri e gli attacchi fossero al 100% compatibili con le soluzioni tecniche adottate sulla macchina prodotta dal cliente.
A seguito dell’esito positivo di tutti test preliminari, si è proceduto alla produzione in serie del componete che è diventato lo standard in quella particolare linea di macchinari prodotti dall’azienda cliente.
Vantaggi reali e misurabili
Il cliente ha così ottenuto in tempi rapidi (meno di un anno dall’analisi preliminare alla produzione in serie) un giunto rotante unico, utilizzabile per tutti i diversi fluidi grazie alla tenuta meccanica interna che può essere agilmente cambiata. La standardizzazione ha ridotto il numero di codici da gestire a magazzino, mentre le modifiche strutturali hanno ridotto drasticamente i tempi di montaggio e le necessità di manutenzione.
“Il cliente ha apprezzato soprattutto il nostro approccio pragmatico e finalizzato a ottenere un concreto vantaggio in termini di tempi ridotti e risparmio di costi”, ha concluso Corigliano.
Gli investimenti di Johnson-Fluiten nell’offrire progetti su misura portano a risultati tangibili in termini di soddisfazione e fidelizzazione del cliente; dopo aver sperimentato l’approccio risolutivo dei problemi proposto da Johnson-Fluiten, i clienti mostrano una ridotta propensione ad accontentarsi della semplice vendita di un prodotto.
La strategia di impegnarsi per fornire vantaggi concreti e a lungo termine al cliente si è dimostrata nuovamente vincente per Johnson-Fluiten.
Dal 2003 Johnson-Fluiten progetta e realizza giunti rotanti per applicazioni con aria, olio, acqua e altri fluidi. La vasta gamma di soluzioni a catalogo si arricchisce costantemente con soluzioni personalizzate, realizzate in tempi brevi lavorando in partnership con il cliente per rispondere perfettamente a ogni esigenza della produzione. I giunti rotanti Johnson-Fluiten sono utilizzati in tutti i segmenti dell’industria meccanica e disponibili con le certificazioni richieste dai diversi settori. Per ulteriori informazioni sulle soluzioni Johnson-Fluiten, è possibile contattare l’azienda telefonicamente al numero +39 02 3394091 o via mail (info-jf@johnson-fluiten.com), o visitare il sito johnson-fluiten.com/it/.
_______________________________________________________________________
Long-term, tangible benefits
From Johnson-Fluiten a customised rotary joint to improve performance of take-off and stretching cylinders
The collaboration between Johnson-Fluiten and the engineering department of a plant manufacturer revealed the possibility of modifying the rotary joints in use to improve the efficiency of the machinery. This was a team effort requiring careful study combined with the ability to think out of the box. The results more than repaid the energy and creativity invested in completing the project.
Suppliers of fluid handling components manufacture products suitable for most machine builders, but not all of them are able to tailor their solutions to perfectly match specific application needs, providing concrete and measurable benefits.
Johnson-Fluiten has a long history of success in this regard, the most recent example being the development of a special rotary joint for a major international manufacturer of plastics processing machinery.
Complex machines
The manufacturer already used Johnson-Fluiten rotary joints for various plants: their versatility allows for easy integration into various types of machinery, such as calenders, preheaters, riser units, embossers, coolers and take-off and stretching cylinders.
In the latter type of equipment, the rotary joints are assembled in such a way as to deliver the fluids which regulate the temperature of the cylinder, allowing the various stages of plastic processing to take place. These elbow joints must have a perfect mechanical seal in order to convey the fluid through a rotating part; it must also be possible to easily replace the internal mechanical seal so that different types of fluid – diathermic oil, superheated water, water for cooling – can be used without changes to the production line.
From Johnson-Fluiten’s catalogue, the customer had selected the SX joints produced by Kadant, to which they applied space-saving assembly heads, made by the manufacturer itself to fit the joints into the machinery: the performance of the joints was very good, but the adaptation of the inlet and outlet connections required additional machining, which reduced the overall efficiency of the process.
A proactive partner
Johnson-Fluiten’s relationship with customers does not end with the delivery of components, but continues to ensure that the delivered solutions are perfectly adequate and that improvements can be made if necessary. “We realised that the SX joint, although adequate, did not have the perfect match with customer requirements which we are accustomed to ensuring,” Ilvio Corigliano, Sales manager at Johnson-Fluiten, explained.
Working side by side with the customer’s designers, Johnson-Fluiten’s engineers devised a solution which retained the advantages of the SX joint – the ability to be used with different fluids, perfect sealing and virtually zero maintenance – while eliminating the need for adaptation during assembly. In view of the customer company’s production volumes, Johnson-Fluiten considered creating a customised joint. “We concluded that the work of prototyping, testing and producing a custom joint would be an effort more than justified by the unquestionable benefits the finished product would bring to the manufacturer,” Corigliano continued.
Customised design
The technical team identified a solution enabling them to eliminate any need for adaptation during assembly and greatly simplify this operation by increasing the length of the rotor by 20 mm and designing a fully customised head to suit the size and specification of the machine.
During the design phase, Johnson-Fluiten engineers considered the possibility, following the modifications made to the head and rotor, of using an RX joint in place of the SX joint in use: the new configuration made it possible to use this model despite the reduced dimensions required by the take-off and stretching cylinders.
The use of this component proved to be particularly efficient in this application: the RX joint uses bearings instead of graphite bushings, which significantly reduced friction and made it possible to achieve the required rotation speed even with a lower-power motor, thus saving energy.
After the necessary surveys and preliminary tests, a prototype was produced under very tight deadlines to verify that the dimensions, overall footrpint and connections were 100% compatible with the technical solutions adopted on the machine produced by the customer.
Following the positive outcome of all preliminary tests, the supplier proceeded with the mass production of the component, which has become the standard in that particular line of machinery manufactured by the client company.
Real and measurable benefits
The customer thus obtained a single rotary joint suitable for all different fluids thanks to the internal mechanical seal which can be easily changed; the whole process took less than a year from preliminary analysis to series production. Standardisation reduced the amount of part numbers to be stocked, while structural modifications drastically reduced assembly time and maintenance requirements.
“Above all, the customer appreciated our pragmatic approach aimed at achieving a concrete benefit in terms of reduced time and cost savings,” Corigliano concluded.
Johnson-Fluiten’s investment in offering tailor-made projects leads to tangible results in terms of customer satisfaction and loyalty; after experiencing Johnson-Fluiten’s problem-solving approach, customers show a reduced propensity to settle for the simple sale of a product.
The strategy of striving to provide concrete, long-term customer benefits has once again proven successful for Johnson-Fluiten.
Johnson-Fluiten has been designing and manufacturing rotary joints for air, oil, water and other fluid applications since 2003. The wide range of solutions in the catalogue is constantly being expanded with customised solutions, realised in short lead times by working in partnership with the client to perfectly meet every production requirement. Johnson-Fluiten rotary joints are used in all segments of the mechanical engineering industry and are available with the certifications required by the different sectors. For more information on Johnson-Fluiten solutions, you can contact the company by phone on +39 02 3394091 or by email (info-jf@johnson-fluiten.com), or visit johnson-fluiten.com/it/.