ifm ha supportato Refresco e Tetra Pak in un progetto di digitalizzazione “greenfield”
Il Gruppo Refresco è leader per l’imbottigliamento di bevande analcoliche in Europa.
In qualità di co-packer, l’azienda imbottiglia le bevande analcoliche di numerosi produttori di marchi famosi in bottiglie e confezioni di cartone.
Solo in Francia, l’azienda gestisce quattro impianti di imbottigliamento, di cui uno presso il sito di Le Quesnoy.
Per soddisfare la crescente domanda di entrambi i tipi di confezioni in modo ancora più efficiente, Refresco ha deciso di costruire un nuovo stabilimento nel nord della Francia con una capacità di imbottigliamento di 30.000 bottiglie PET e 8.000 cartoni all’ora.
Progetto di Digitalizzazione: Creando il Futuro da un Foglio Bianco!
“Per noi è stato chiaro fin dall’inizio che volevamo un edificio all’avanguardia e soprattutto sfruttare i vantaggi della digitalizzazione”, afferma Joseph Kerdo, Project Manager di Refresco France e responsabile della progettazione del nuovo impianto.
Per realizzare la fabbrica in rete, l’azienda ha lavorato a stretto contatto con ifm, partner per la digitalizzazione e con Tetra Pak, responsabile della costruzione delle linee di imbottigliamento.
“ifm ci ha supportato nel progetto fin dall’inizio, suggerendo le soluzioni giuste e rispondendo a tutte le nostre domande”, spiega Grégory Crozier, Automation Team Leader di Tetra Pak.
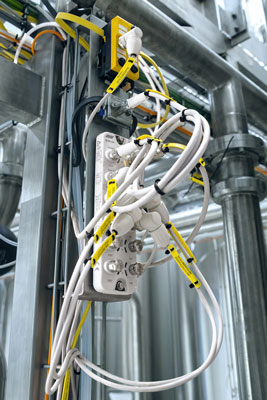
AS-i e IO-Link per la trasmissione digitale dei dati
È stata progettata un’infrastruttura con IO-Link e AS-i per un affidabile scambio digitale dei dati.
Il vantaggio di IO-Link rispetto al cablaggio analogico è il raggruppamento decentralizzato delle informazioni dei sensori tramite i master IO-Link installati sul campo, ai quali i sensori sono collegati tramite cavi a 5 poli standardizzati e non schermati. Questo semplifica il cablaggio e riduce il potenziale di errore nel collegamento dei sensori. Poiché la trasmissione dei dati è esclusivamente digitale, i dati di misura non vengono alterati dai processi di conversione. Neanche le interferenze EMC possono influenzare le informazioni.
“IO-Link e AS-i semplificano notevolmente l’architettura dei dati”, afferma Grégory Crozier
“I dati sono sempre disponibili e il cliente beneficia di una manutenzione facile e affidabile perché le opzioni di diagnostica sono migliori rispetto al passato.
Un altro vantaggio è la semplice sostituzione dei componenti senza necessità di nuove programmazioni”.
Semplice, flessibile, versatile
AS-i viene utilizzato per il collegamento delle valvole e il livello di processo. Grégory Crozier ne spiega le ragioni: “Per noi, AS-i offre il vantaggio di una pianificazione semplice e ben preparata e di un’implementazione altrettanto facile”. AS-i mostra i suoi vantaggi soprattutto per il collegamento di punti dati ampiamente distribuiti. Per la trasmissione dei dati e l’alimentazione dei sensori collegati è sufficiente un cavo piatto a due fili. La lunghezza del cavo può raggiungere i 1.000 metri se si utilizzano cavi e ripetitori standard. Distanze maggiori fino a 3.000 metri possono essere collegate utilizzando cavi in fibra ottica. I sensori e i master possono essere collegati al cavo AS-i in modo flessibile e preciso in qualsiasi punto grazie alla tecnologia di perforazione dell’isolante. Un altro vantaggio: AS-i può essere combinato con IO-Link, come nel caso del progetto Refresco. I sensori decentralizzati dei singoli componenti dell’impianto vengono raggruppati tramite master IO-Link compatibili con AS-i e poi trasmessi al PLC e al livello IT tramite l’infrastruttura AS-i. Anche le applicazioni di sicurezza, come il monitoraggio dei portelli, possono essere implementate con AS-i grazie alla gamma di prodotti per la sicurezza.
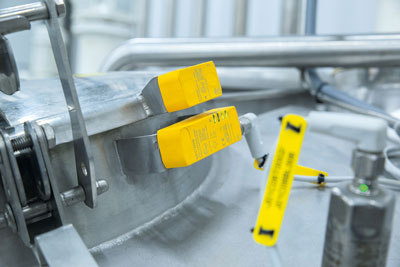
Conclusioni
Grazie alla flessibilità e facilità di gestione di IO-Link e AS-i, Tetra Pak è stata in grado di pianificare e implementare la digitalizzazione degli impianti di imbottigliamento per il progetto Refresco Bluebird in modo rapido e semplice.
Anche Refresco ne trae vantaggio: informazioni più precise sui sensori, migliori possibilità di diagnostica e manutenzione più semplice.
“Per noi AS-i offre il vantaggio di una pianificazione semplice e ben preparata e di un’implementazione altrettanto facile.”
“ifm ci ha supportato nel progetto fin dall’inizio, suggerendo le soluzioni giuste e rispondendo a tutte le nostre domande.”
Video applicativo https://youtu.be/vDGz4b_21SQ